Global Chip Shortage - How Beta Solutions has adapted
Date: July 27, 2022
Introduction
Since 2008 Beta Solutions Ltd has been privileged to provide electronic design and production solutions for our clients. During this time (like many businesses) there have always been challenges* and opportunities, and learning to adapt has been essential.
Our most recent significant challenge has been the global chip shortage. If you haven’t already, refer to our previous blog “Global Chip Shortage - Why We Are In This Crisis”, to learn more about what this crisis is and the causes behind it.
As Andy Grove once said of business: “There are two options: adapt or die.” Needless to say - we have chosen to adapt(!) and this blog provides answers to the following questions:
- How have we adapted to the challenges faced by the global chip shortage?
- What are the implications for our clients?
- How long will these adaptations last?
*For example, commencing business during the GFC in 2008!
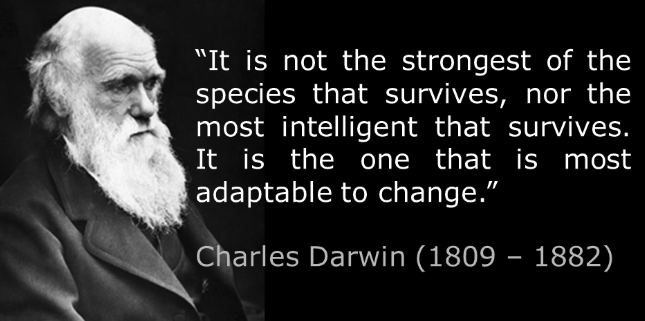
How have we adapted to the challenges faced by the global chip shortage?
Design Process - Traditional approach pre-shortage
Research and Development (R&D) can be a complex process, and the more Research that is required - the more convoluted this process will be. (This is because Research by definition contains an element of uncertainty).
Suffice to say that the R&D process does not always follow a nice water-fall project flow - where the tidy completion of one stage then leads to the commencement of the next phase.
That said, in very simplified terms, our hardware design process would generally follow these following phases:
- R&D - Architecture and Specification
The project is scoped out, and a “block level” preliminary design and specification is formed.
“Key components” are identified and a general risk assessment is performed.
An example of a key component would be a motor driver for a project that contains one or more motors. Most projects also include a microcontroller, which is also categorized as a key component. - R&D - Design Schematics
This is where our engineers take the block-level design and transform this into an actual meaningful logical circuit design in CAD.
Key components are (mostly) locked-in and all the other components are selected. - R&D - Design PCB
Whereas the previous phase is concerned with establishing the logical function of the electronics, the PCB design phase is where the actual circuit board is designed in CAD. - R&D - Prototyping and Testing
Components are ordered along with the bare PCBs - enough for a few prototypes to be made. We build enough boards for hardware and firmware verification
R&D - Design Iterations (If required)
For all but the most simple PCBs, it is reasonably common practice to make some optimisations to the design after testing and prior to going into production. - Production
The R&D phase is complete and we move into production, where the Bill Of Materials (BOM) is generated and production files are finalised. All components are then procured, and the PCB is fabricated!
NB: This entire process from Phases 1-6, could (usually) take anywhere from 6 - 24 months depending on the complexity of the project.
Look to our blog for upcoming articles about our R&D process in more detail.
Design Process - New (Adapted) approach post-shortage
Downside of Traditional Approach
While our traditional approach has worked well in the past, due to the global chip shortage, the problem is that the components that are selected during the architecture and design schematics stages could well be out-of-stock by the time the PCB is ready for production.
For a circuit board to work as intended, all intended components must be present. If a single component is unavailable, the production of an entire PCB (sometimes consisting of several hundred components) will be stalled.
Some electronic components have manufacturer lead times of 26 - 72 weeks(!).
New Adapted Approach
Clearly it is not acceptable to unexpectedly have to wait for this length of time before receiving their products to sell, so we have adapted our process to include the following three changes:
- Ordering in Advance
We now aim to procure production component stock immediately after the Design Schematics Phase. This comes with an element of risk, especially considering the prototyping phase has not been completed at this stage and components may be required to change.
However, this is a risk that many of our clients are willing to accept, given that the alternative is to simply “roll the dice” and see if components will be available at production time. - Additional consideration in component selection
Traditionally components are selected based on function, price, availability and physical properties such as size and/or temperature range. Selection criteria has grown now to include drop-in-replacement alternatives, generics, and stocking history.
For example, it is often now more attractive to consider more highly priced components with a better supply chain, over cheapest parts that have excessively long lead times. - Design for alternatives
Sometimes there are component alternatives that are a drop-in-replacement (components that have a different part number, or even made by a different manufacturer, that will fit into exactly the same space on the circuit board). However, while these can be common for simple components (resistors, capacitors etc), for more complex components, this can be difficult or not possible.
Therefore, a board can be designed that works with one of two possible components depending on stock at the time of production or future production runs. These can be selectable by placing certain supporting components or not.
Overview: Traditional Vs Adapted Design Phases
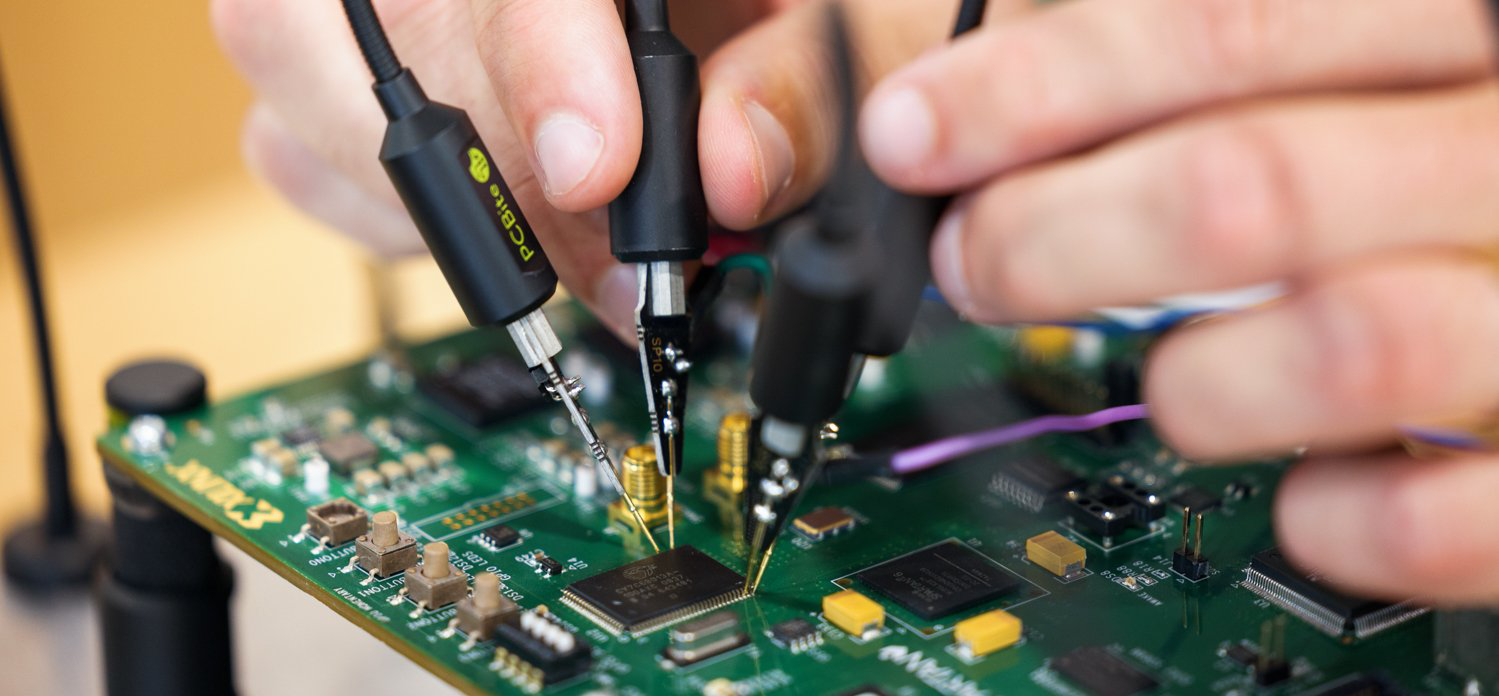
What are the implications for our clients?
Andy Grove’s quote again (“There are two options: adapt or die”) can be taken quite literally in a business sense. If our customers do not have stock to sell - and therefore the ability to trade - there is every possibility they will have to permanently close their doors.
Despite the Global Chip Shortage, we have been able to change the way we undertake product development - which largely mitigates the impacts (especially the excessively long leadimes) on our customers.
That said, there are some implications that our clients should be aware of, these being:
- Cash Flow
R&D is an investment and as such there is a capital outlay required. Moreover, not only does the client have to fund the R&D process, they also have to fund Production. Together and R&D and Production form the “Total Project Capital Outlay”.
Regarding the two different approaches (Traditional Vs Adapted) - the Total Project Capital Outlay doesn’t significantly change. However, what does change is when the Capital is expended - which is known as Cash Flow.
Previously, Production Costs were incurred at the time of manufacturing - in essence, at the end of the project). Now a sizable portion of these costs have shifted and are incurred much earlier in the design process, meaning our clients need to have such funds in place. - Implications on Risk
As previously mentioned, the lowest risk approach is to wait until the R&D phase is ABSOLUTELY COMPLETE, prior to ordering Production Stock.
Ordering Production Stock prior to the completion of the R&D phase does always carry some risk - as any changes to the design may mean that pre-purchased stock may no longer be required for production. In this instance the customer would have incurred a “sunk cost”.
However, this is a calculated risk that many of our customers are willing to accept - given the extremely long lead time alternative!
[2] There are likely some increased overheads with the Adapted Approach - due to (for example) additional freight for the components. Also, if components have been ordered, and then later deemed to be non-needed, these components could be a sunk cost.
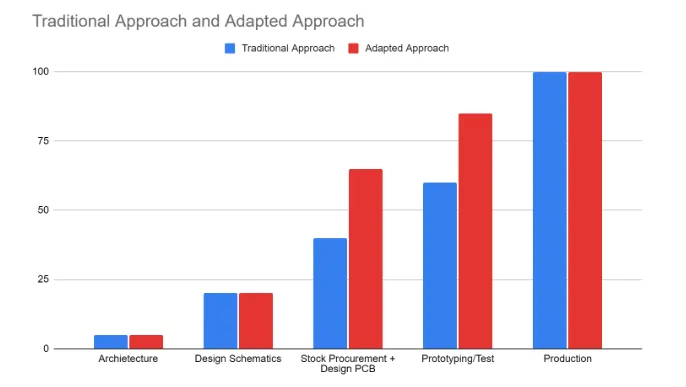
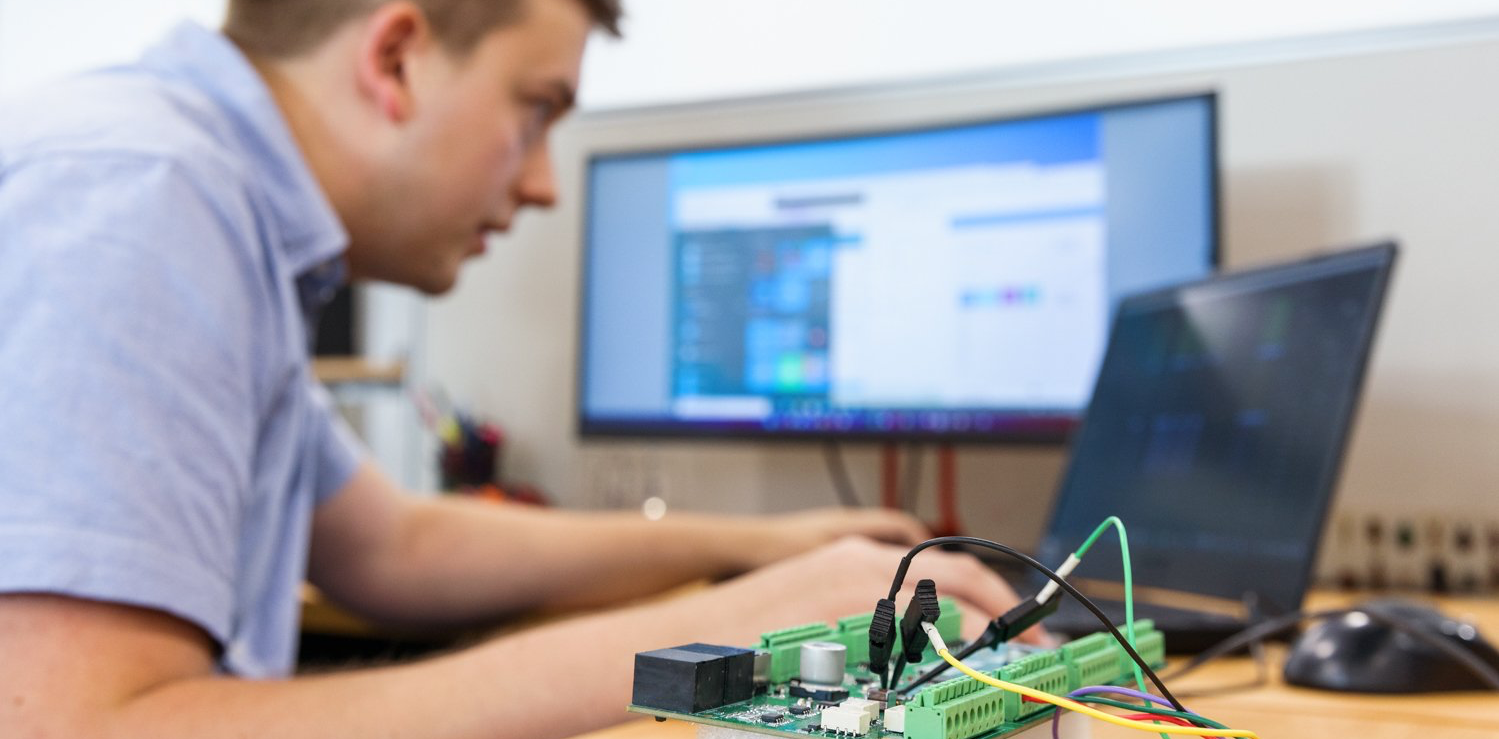
How long will these adaptations last?
Analysts predict an easing in the second half of 2022 as demand-supply gaps decrease. Semiconductor and component research analyst William Li said just recently that “coupled with wafer production expansion and continuous supplier diversification, we have witnessed significant improvement in the component supply situation, at least in the first quarter.”
For the moment though, the global tech supply chain remains uncertain. Manufactuaring the chips used to make our electronics and consumer goods, still depends on the stability of our world. As we still manage a global pandemic, implications of lockdowns with ongoing Covid waves, and the effects of the war between Russia and Ukraine and the supply of neon*, we are not on the home straight as yet.
*Neon is a colourless and odourless gas, and plays a vital role in the manufacturing of the tech that we use everyday.
Conclusion
Here at Beta Solutions the Global Chip Shortage has resulted in us changing the way we execute our R&D and Production projects. Our new (adapted) approach has meant that we have largely mitigated the most deleterious effects of the crisis - enabling our customers to still meet their target production schedules.
Our new (adapted) process remains for the foreseeable future - at least for another few years - to benefit our clients, both in the way we undertake product development, and how we largely reduce the impacts of long lead times and risk to our customers.
We would love to talk to about any potential new R&D electronics projects, or concerns you may have about the implications of the Semiconductor shortage to your business. Please do get in touch with us!
References:
- Analysts Predict End is Near for Global Chip Shortage https://www.tomshardware.com/news/analyst-predicts-end-of-chip-shortage
- The neon shortage is a bad sign https://www.vox.com/recode/22983468/neon-shortage-chips-semiconductors-russia-ukraine