Touch Screen LCD Controller
Over the past decade, Beta Solutions has proudly partnered with Thermoplastic Engineering (TPE), working hand-in-hand to create cutting-edge control solutions for their state-of-the-art fume cupboards. You can read about the previous fume cupboard projects
here.
As time progressed, the demands for these fume cupboards have evolved, necessitating the integration of diverse controllers and numerous custom adjustments to deliver a truly tailored experience for each client. Thermoplastic Engineering entrusted Beta Solutions once again to enhance their world-leading product offering, focusing on the following objectives:
- Transitioning from a 4 line character display to a sophisticated touch screen and touch glass LCD user interface.
- Streamlining several controllers into a single "Unified Controller" PCB with multiple hardware and software configurations, to boost cost efficiency, and simplify the setup and user interface.
- Incorporating eco-friendly features for energy conservation and increased versatility to cater to a broader clientele.
- Integrating a BACnet interface for seamless connectivity with Building Management Systems (BMS).
Our specialist hardware engineers at Beta Solutions assessed various feasible solutions to achieve these goals. An architecture was designed which resulted in the development of the Unified Controller and Unified Display.
Both the new controller and display products have been met with positive feedback from TPE's customers, expressing satisfaction with the upgraded system!
In the following sections of this project writeup, we dive deeper into various aspects of this successful collaboration with Thermoplastic Engineering, exploring in detail:
- The Unified Controller: An overview of its development, features, and functionality.
- The Unified Display: A look at its design and user-centric interface.
- Quality Assurance: How we ensured quality in design and production.
- The Collaboration Success Story: A testament to the partnership between
Beta Solutions and Thermoplastic Engineering, and the positive impact of our joint efforts.
Figure 1: Fume Cupboards
The Unified Controller
The Unified Controller lies at the core of the fume cupboard system, functioning as its "brains" by managing overall control and performance. In conjunction with TPE, our team carefully designed it to not only support numerous inputs and outputs but also withstand electrical transients and harsh chemical atmospheres commonly encountered in fume cupboards.
The controller's tight management over every aspect of the fume cupboard significantly enhances user safety. Building managers appreciate the energy-saving features, such as the auto-closing sash when no users are detected, allowing for a reduced air extraction flow rate and minimized air conditioning load on the building. This efficiency leads to significant cost savings for laboratories.
The EcoAir controller feature maintains a constant face velocity regardless of the sash height by actively monitoring it and adjusting the fan speed accordingly. This capability ensures greater HVAC efficiency and additional energy savings.
In addition to automatically increasing fan speed when detecting reduced airflow, the controller operates in four stages: pre-purge, ready to use, post-purge, and standby. It instantly responds to any abnormal conditions to ensure maximum user safety.
The Ecosash feature further contributes to laboratory safety by automatically lowering the sash after a predetermined period of inactivity, minimizing conditioned air extraction levels. This versatile feature is easy to use and configure, automatically stopping when obstructions are detected.
Figure 2: The Unified Controller
The Unified Controller seamlessly combines the functionality of three separate products into one integrated solution, which includes the following hardware functions:
- Analog-to-Digital Converters (ADCs) for continuous monitoring of
- Airflow
- Sash height
- User presence via proximity sensors (PIR)
- Digital-to-Analog Converters (DACs) for precise PID control of
- Fans
- Dampers
- BMS signaling
- Servo motor control or similar motor control for automated sash raising and lowering
- Digital inputs and outputs for real-time monitoring and control of variables such as:
- Personnel occupancy
- Airflow
- Sash height
- Sash obstructions
- Temperature
- Emergency stop status
- Alarm inputs
- RS485 interfaces for BACnet protocol integration with BMS and communication with the Unified Display.
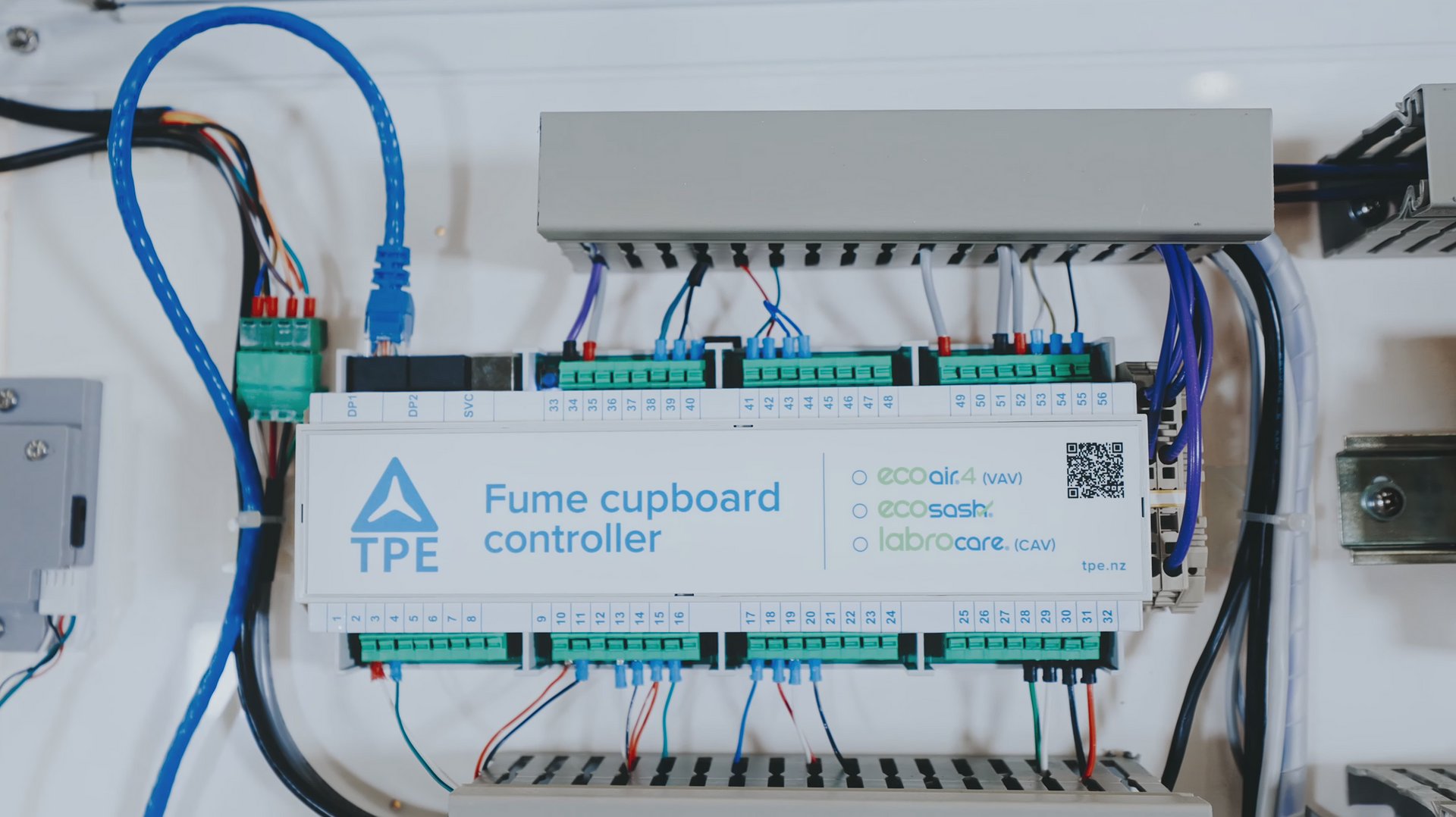
The Unified Display
Figure 4: Unified Display main status screen
The Unified Display is a custom display assembly including:
- Custom designed glass touch sensor
- High brightness LCD display
- A printed circuit board (PCB) containing:
- A Microcontroller - to run the firmware and interface to the display and touch sensor
- An energy storage - to ensure users can be notified of a safety event if building power is lost
- A buzzer - to provide audible feedback to user interactions
- A CNC machined mechanical plastic frame
The Human-Machine Interface (HMI) for the Unified Controller is an intuitive touch screen LCD display, offering superior visibility in all laboratory conditions. Our software team leveraged the Light and Versatile Graphics Library (LVGL) to develop a flexible, modern display.
The display boasts user-friendly features such as:
- Responsive touch screen experience, including with gloved hands.
- Main display screen for cupboard status.
- Customizable standby screens.
- Password-protected settings screens.
- Adaptive cupboard configuration settings.
- Interactive calibration screens that provide clear instructions for various configurations.
Production Quality Assurance
Beta Solutions Ltd are privileged to manage the production of both the Unified Controller and Unified Display. Learn more about our production services here.
Figure 5: Unified Controller test jig. Used to validate the electronics during production.
To control and monitor quality, each product undergoes full functional testing during production before integration into fume cupboards. A production test rig (shown above) was designed and built that uses a bed of nails system for thorough and rapid electronics testing, which not only builds confidence in the quality of outgoing goods but also optimizes production efficiency.
Success
Our partnership with Thermoplastic Engineering on the fume cupboard project has resulted in positive outcomes and customer satisfaction. The project's continued success reaffirms our commitment to devise winning solutions in collaboration with our clients.
If you require touch screen displays or electronics/firmware expertise for your project, we would be delighted to assist. Let's discuss your needs and explore how our team can contribute to your success. Contact us today to start the exchange—we're eager to learn more about your objectives!
For more information on Thermoplastic Engineering's fume cupboards, visit their official website:
https://thermoplastic.co.nz/
Client Testimonial
"I am glad to have worked with Beta Solutions on our Ecoair®4 fume cupboard controller development. They have been a great fit for TPE, having a wide skillset to deliver a very complex development and achieve good quality, plus lean and fast service that has worked well with our budgets. We have worked with them repeatedly from initial concept through to mass production, on the way leveraging their partnerships with suppliers, for example in industrial design and procurement.
On this Ecoair®4 development they provided good feedback and discussion on our initial requirements specification before using it to generate a thorough proposal for us. Once we were underway, they worked quickly to de-risk some key technical challenges including glass touchscreen design and procurement, our multi-device software update architecture, and the securing of critical components in the middle of a Covid pandemic.
We worked with Beta’s industrial designer to realise our vision of a simple, elegant graphic UX design to share between a combination of colour display and touch buttons, which Beta implemented in the LVGL software and glass production. Through the main software development, we acted as Beta’s testing partner, writing the test methods and progressively working with Beta to get the software to the finish line. We used a variety of full-scale Fume Cupboard test beds at our own factory, at Beta solutions, and at some customer facilities. This phase was the most intense for us and thankfully we had good momentum, communication, and delivery in our sprints with Beta. We used Beta’s testing documentation systems, a team slack channel, video calls and two-way sharing of our test data. We realised a need to add several extra functionalities by variation, which Beta did quickly and easily.
Only seven months from completion we are already ordering our fourth production run, and the controller is performing extremely well in quality lab facilities throughout the country such as Victoria University of Wellington, the new AgResearch Lincoln building, and the University of Auckland’s Building 201 refurbishment.
I would like to thank Beta solutions for being great to work with and delivering us a very sophisticated, high quality and good value solution for our customers."
Andy Gow
Thermoplastic Engineering Ltd (TPE)
* All the content in this article, including imagery, has been approved by our client for publication on this website.